Preventing Disaster in Petrochemical Facilities
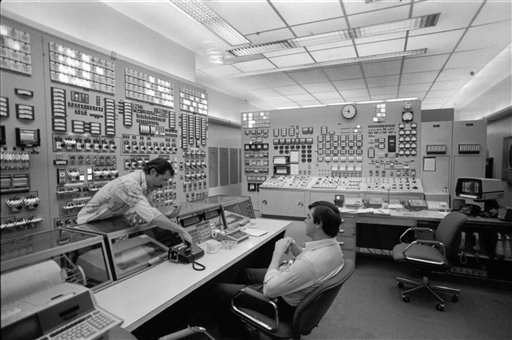
May 10, 2011 - asmag.com
Our present world relies heavily on both oil and gas to sustain our required levels of daily energy consumption. Despite the recession and the recent debates regarding extensive oil usage due to both economic and environmental concerns, the oil and gas industry continues to grow and expand while reliable alternative sources of energy have yet to be found. According to PricewaterhouseCoopers in the U.S., a total of 39 business deals within the oil and gas sector were reported and made in a span of three months since July 2010, with a value totaling US$17.6 billion. Due to the combustible nature of oil, gas and other chemicals, these facilities must be fully equipped to prevent a disaster. A fully integrated system can allow for faster response times during emergencies. Everyone who enters and exits the facility must be fully authorized by means of a secure access control system since these facilities are prime targets for sabotage. Should an accident or miscalculation occur, it can result in a tremendous loss of life as well as negatively affect both the business and the environment, as seen in the disastrous Macondo well leak.
Oil and gas security witnessed an increase in market demand, but was not immune to the recession. “Many projects that have been planned for a number of years lost their funding,” said Bjorn Songe-Moller, VP of Sales for Scandinavia and Russia, IndigoVision. “However, the recent attention paid to terrorist threats has alerted companies to the necessity of improving and upgrading existing security systems, as well as adding new advanced systems for their production and transport facilities.”
Security measures must cover all the stages of the project, starting from the planning, construction, implementation and operation, to abandoning, said Evgenia Ostrovskaya, Global Business Development Director for Axxon.
Special attention is required during construction. “Oil and gas companies have identified several points in their operation whose disruption would have an enormous impact on the company's operation,” said Vincentius Liong, Director for Samudra Buana Texindo. Critical locations include production facilities; distribution and storage facilities; and the IT building, which houses the control room — the system's heart.
Risk assessments identify which places need more security. “Each critical area is classified into five color categories: low risk (green), guarded and general risk (blue), elevated and significant risk (yellow), high risk (orange) and severe risk (red),” Liong said. “The classification of each area is done by performing a security vulnerability assessment, which helps form a standardization when deploying security equipment.”
Along with prioritizing risk, each zone has unique monitoring requirements. “Zone monitoring provides up-to-date information on who is on-site for safety and security reasons, and offers a real-time display and numerical counter of every individual in a predefined zone within the building or site,” said Philip Verner, Sales and Marketing Manager, CEM Systems (a Tyco International company). “This is suitable for use in high-risk sites where evacuation may be necessary, or in buildings with capacity restrictions on certain areas.”